Metal machining is capital and labor-intensive business. It demands expenses on several resources like raw material, process equipment, tools, etc. Therefore, every metal product manufacturer looks for cost-cutting tactics in order to grow profit margins and offer products at cost-efficient rates to the customers. This post discusses a few tactics that can help manufacturers to cut metal machining cost without deteriorating the quality of production.
The following tips will help you save on metal machining costs.
With the development of fiber optic technology, many metal manufacturers have begun to choose fiber laser cutting machines for the manufacture of metal workpieces. Although CNC fiber laser machines are highly expensive, CNC metal machining is an efficient technique of production. Therefore, despite the high price of fiber cutting machines, more and more metal manufacturers are beginning to invest and rely on it.
Choosing a high-efficiency fiber metal cutting machine requires a higher cost initially, but investment in the right state-of-the-art equipment is a long term cost-cutting strategy. Generally, this equipment are designed for precision in a specific set of tasks. Due to precision, close tolerance manufacturing can be performed which ultimately reduces waste material. The less the material is required, the lesser is the expense of manufacturing.
In addition, the equipment helps to increase the processing speed of metal workpieces, which saves time. The machining time reduction is an effective way of cost-cutting of metal manufacturing. As time consumption is reduced, the cost of power consumption drops as the machinery runs for less time.
ACCTEK fiber laser cutting machine adopts RAYCUS/IPG laser source with has international advanced laser technology. Equipped with an efficient transmission system by Taiwan high-precision gear rack after grinding process and high-precision linear guide. Advanced Cypcut control system, group into high precision
CNC fiber laser cutting machine. Each metal manufacturing project can be completed efficiently, which is a cost investment with long-term benefits for metal manufacturers.
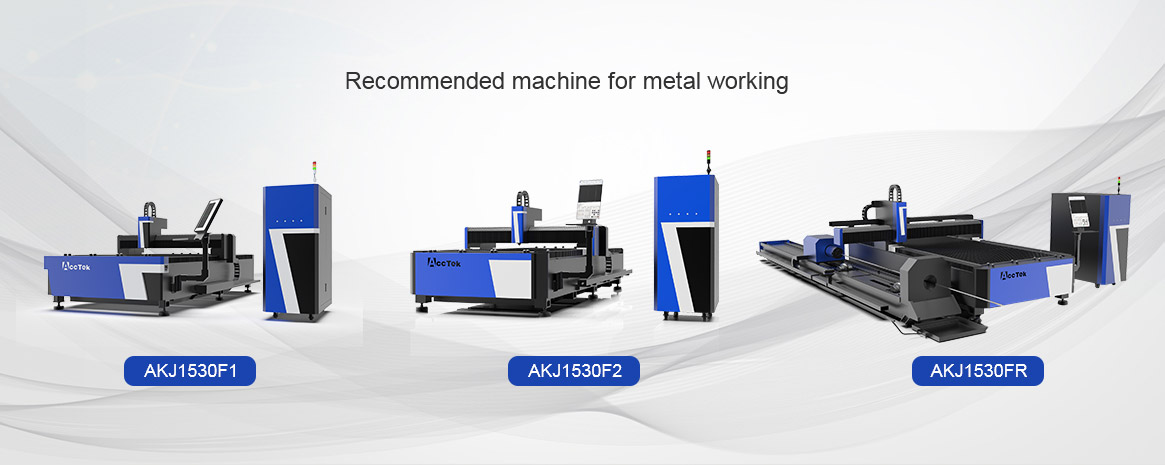
Design for Manufacturing
The first step of metal manufacturing is product design. Each product is designed on specific requirements that are expected to be satisfied in the final product. Therefore, in order to avoid manufacturing errors or manufacturing difficulties, the design must be compatible with manufacturing resources. The design for manufacturing helps in designing the product incompatibility with resources and reduced turn-around time.
Bulk Material Purchase
Bulk material purchase helps in cutting the costs of raw materials. If a small quality purchase is made, the manufacturer might have to pay per piece cost. On the other hand, if the bulk purchase is made, then the chances of cost reduction are high.
Bulk Manufacturing
Bulk manufacturing is a way of cost-cutting. Since bulk manufacturing is a continuous manufacturing process, the halt time is saved in this. This means the time between switching from one product to another is negligible which saves machining time and operational cost.
These are a few cost-cutting tips for metal manufacturing. The tips are not only helpful to the manufacturers but also to the customers. Since most of these tips focus on time-saving, the customer can get the product in a lesser turnaround time.
If you are planning to start a metal cutting project, it is time to choose a
fiber laser metal cutting machine for your workshop.