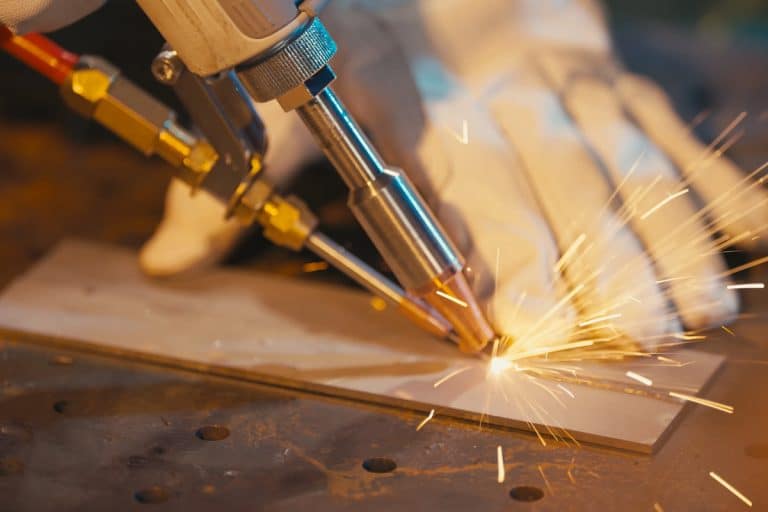
Laser Welding VS MIG Welding
This article compares laser welding and MIG welding in terms of process, applications, cost, quality, and efficiency to help readers understand their key differences.
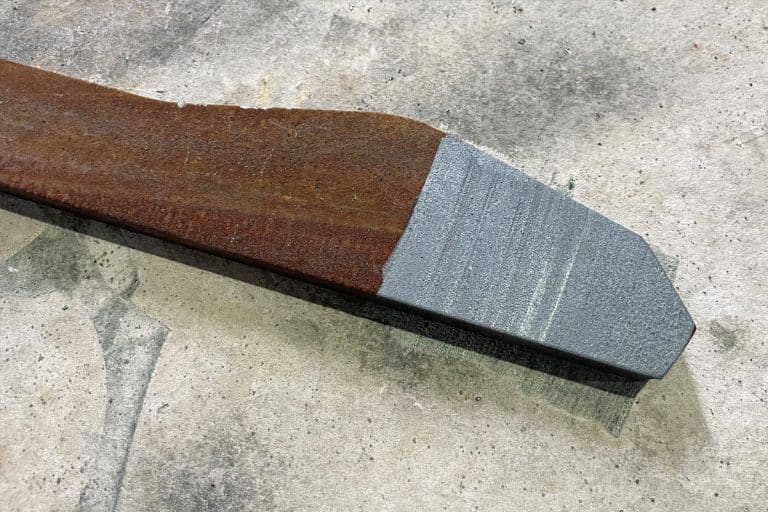
Laser Rust Removal VS Sandblasting Rust Removal
This article compares laser rust removal and sandblasting, examining their working principles, performance, cost, environmental impact, and suitability for various applications.
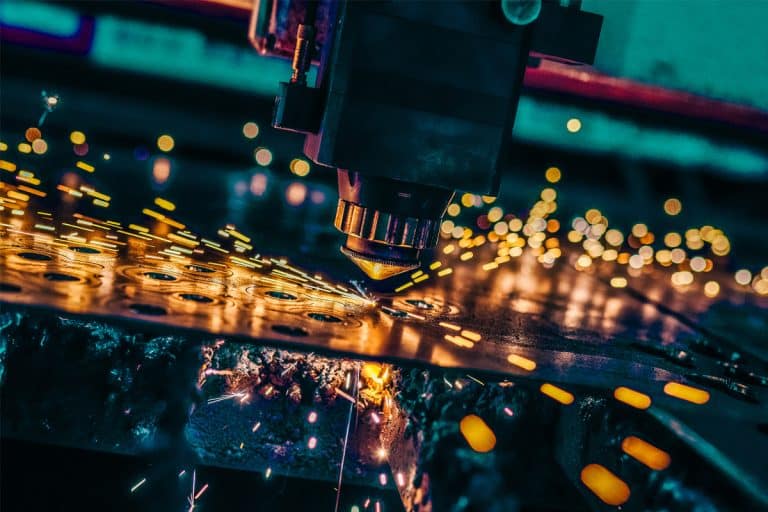
Laser Cutting VS Plasma Cutting: Comprehensive Guide
This article compares laser cutting and plasma cutting technologies, examining their principles, applications, costs, precision, and suitability for different industrial needs.
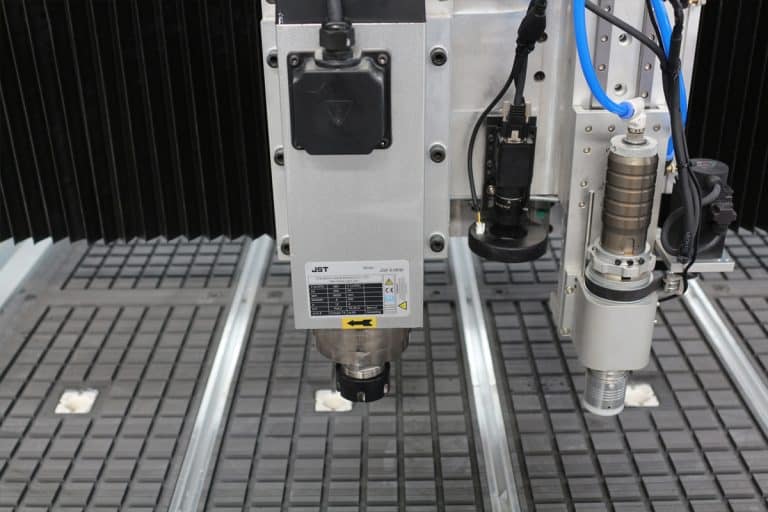
What Is Oscillating Knife Cutting?
Discover the precision, efficiency, and versatility of oscillating knife-cutting technology. Learn how it works, its advantages, its applications, and why industries rely on it.
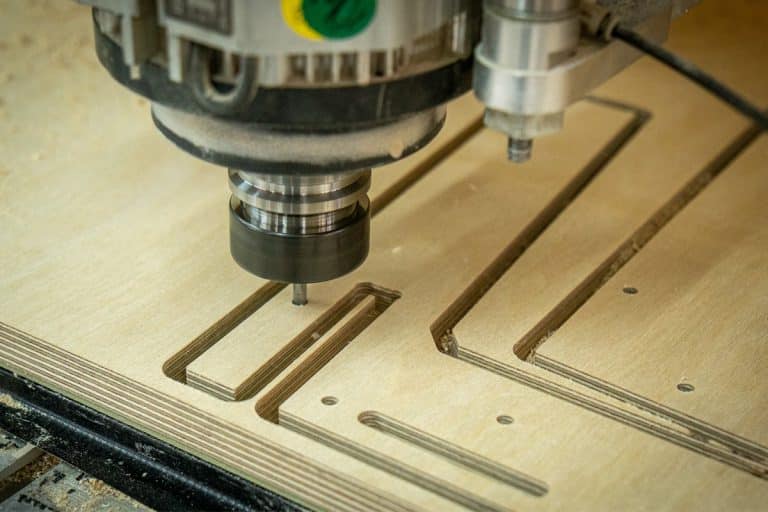
What Is CNC Routing?
Discover the fundamentals of CNC routing, its applications, advantages, challenges, and how advanced CNC technology enhances precision and efficiency across industries.
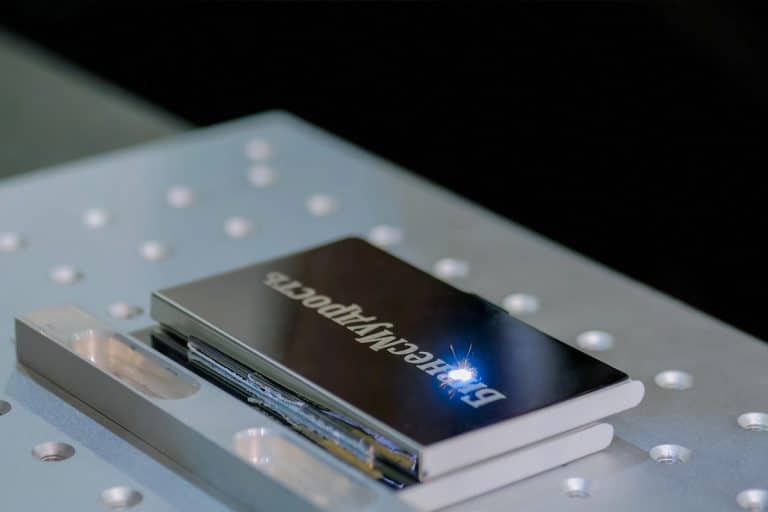
What Is Laser Marking?
Discover the fundamentals of laser marking, its types, applications, advantages, and key considerations. Learn how this advanced technology enhances precision, durability, and efficiency across industries.
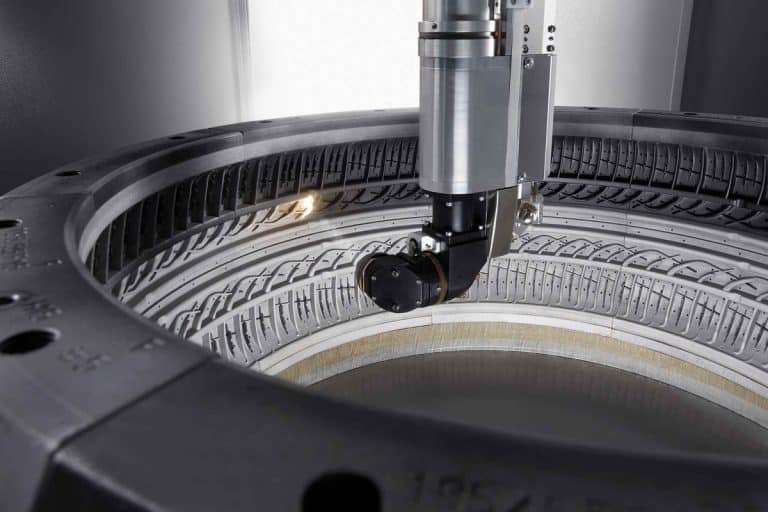
What Is Laser Cleaning?
Discover the power of laser cleaning, an advanced, eco-friendly technology for removing rust, paint, and contaminants with precision. Learn how it works, its benefits, and key applications.
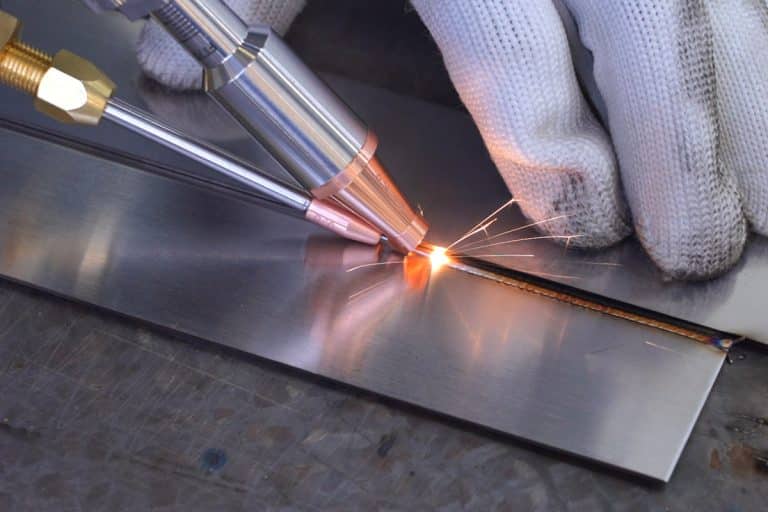
What Is Laser Welding?
Explore the principles of laser welding, its benefits, applications, and how it compares to traditional welding methods. Learn how this advanced technology enhances precision and efficiency.
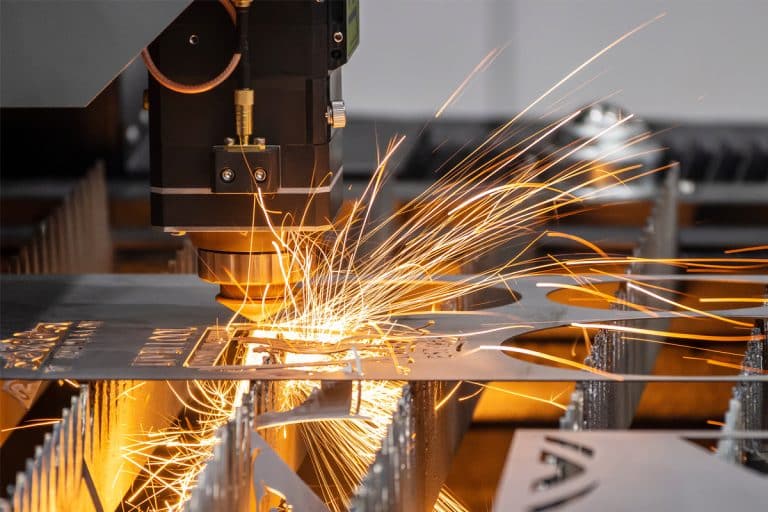
What Is Laser Cutting?
Discover the fundamentals of laser cutting, its process, types, applications, and benefits. Learn how this advanced technology is transforming modern manufacturing.
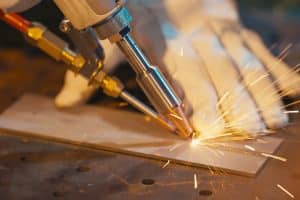
Laser Welding VS MIG Welding
This article compares laser welding and MIG welding in terms of process, applications, cost, quality, and efficiency to help readers understand their key differences.
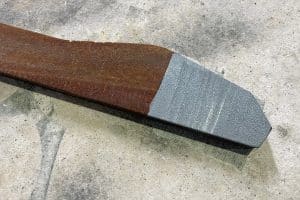
Laser Rust Removal VS Sandblasting Rust Removal
This article compares laser rust removal and sandblasting, examining their working principles, performance, cost, environmental impact, and suitability for various applications.
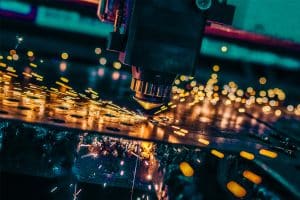
Laser Cutting VS Plasma Cutting: Comprehensive Guide
This article compares laser cutting and plasma cutting technologies, examining their principles, applications, costs, precision, and suitability for different industrial needs.
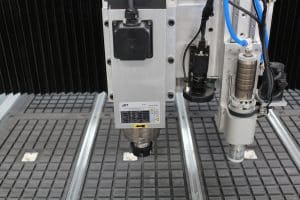
What Is Oscillating Knife Cutting?
Discover the precision, efficiency, and versatility of oscillating knife-cutting technology. Learn how it works, its advantages, its applications, and why industries rely on it.
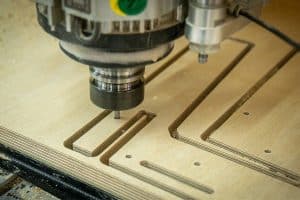
What Is CNC Routing?
Discover the fundamentals of CNC routing, its applications, advantages, challenges, and how advanced CNC technology enhances precision and efficiency across industries.
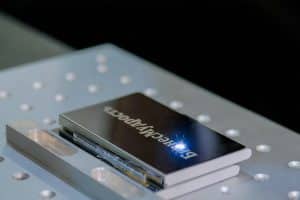
What Is Laser Marking?
Discover the fundamentals of laser marking, its types, applications, advantages, and key considerations. Learn how this advanced technology enhances precision, durability, and efficiency across industries.
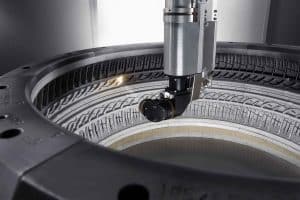
What Is Laser Cleaning?
Discover the power of laser cleaning, an advanced, eco-friendly technology for removing rust, paint, and contaminants with precision. Learn how it works, its benefits, and key applications.
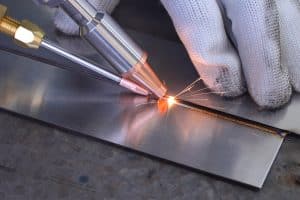
What Is Laser Welding?
Explore the principles of laser welding, its benefits, applications, and how it compares to traditional welding methods. Learn how this advanced technology enhances precision and efficiency.

What Is Laser Cutting?
Discover the fundamentals of laser cutting, its process, types, applications, and benefits. Learn how this advanced technology is transforming modern manufacturing.