The
laser cutting machine is a new cutting equipment in the sheet metal processing industry. It is different from the traditional flame cutting and plasma cutting. The laser cutting machine adopts a non-contact working method, which uses a laser beam to irradiate the surface of the material to make The local temperature reaches the melting point instantaneously, and the coaxial high-pressure gas is used to blow off the slag, forming a fine slit.
Laser cutting machine is a high-speed development of laser technology in recent years. Compared with traditional cutting equipment, it has better cutting quality, lower use cost and longer service life.
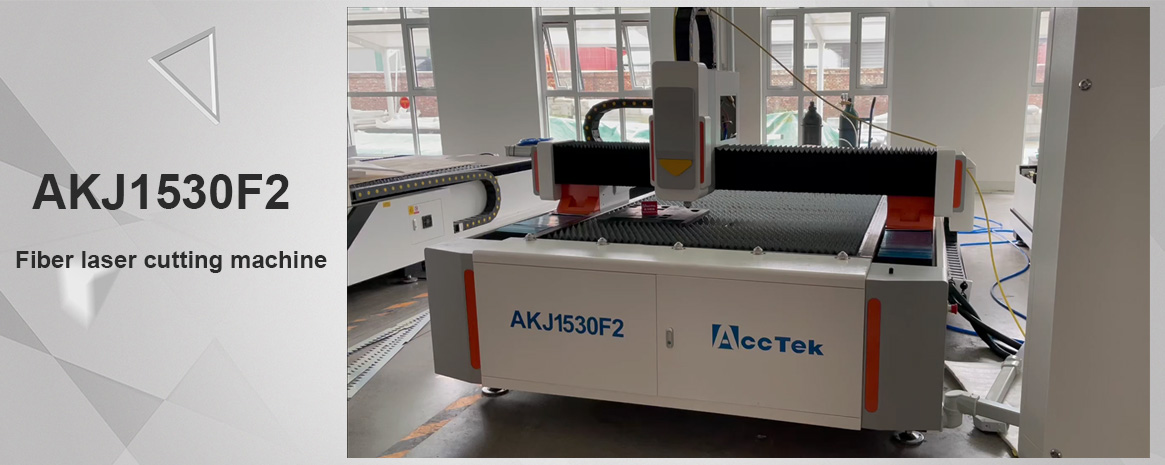
Moreover, the laser of the fiber laser can be transmitted through the fiber, which is convenient for connection with the motion platform and realizes flexible processing, which greatly simplifies the system design of traditional cutting equipment, improves the stability of the system, reduces the amount of maintenance, and is truly suitable for industrial processing applications.
Based on the characteristics of the sheet metal processing industry, most of the processed metal sheets with a thickness of less than 2mm, the optional 500w-700w
fiber laser can cut carbon steel at a speed of 7-8 meters per minute.
Regarding the accuracy of the worktable, considering the accuracy requirements of most sheet metal parts, the positioning accuracy is generally designed to be around 100uM, which also greatly reduces the cost of the bed. Of course, the user can customize the bed according to the material and thickness of the workpiece, as well as the accuracy requirements.
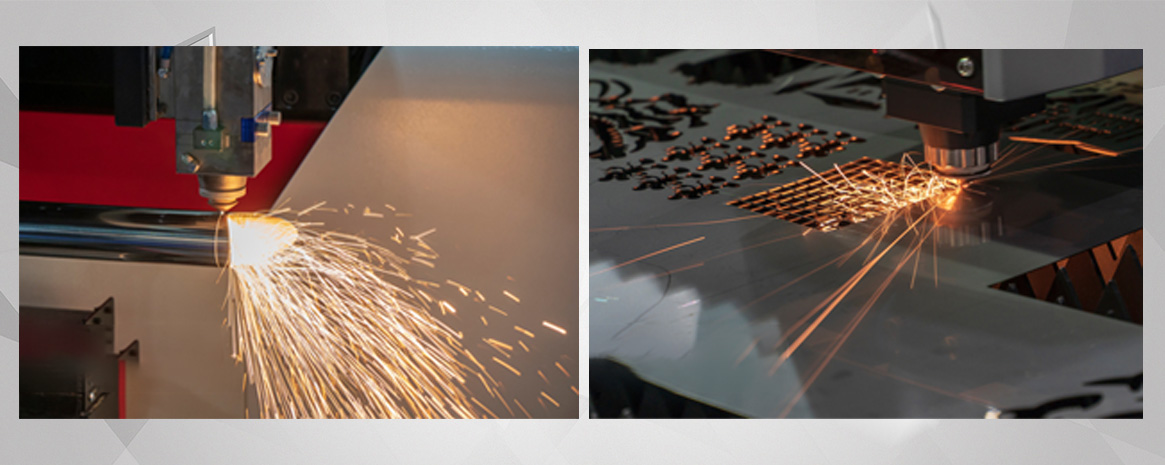
1. The cutting speed is fast, the cutting quality is good, and the cutting precision is high. The workpiece after cutting does not need to be polished and polished.
2. The heat effect of the processed part is small, and the non-contact cutting method does not have any mechanical stress on the material, and the workpiece will not be deformed
3. The operation is simple, equipped with only operating software, you only need to design the cutting pattern in the computer software to automatically cut, especially for responsible graphics.
4. The processing cost is low, generally only a small amount of electricity and gas costs are required
5. It is suitable for various metal materials. Because the energy of the laser beam is very high, it can melt any metal material, especially some metal sheets with high hardness and high melting point.
6. The laser cutting has a high degree of automation, can be completely enclosed, is environmentally friendly, has no pollution, and has low noise, which greatly improves the working environment of the operator.
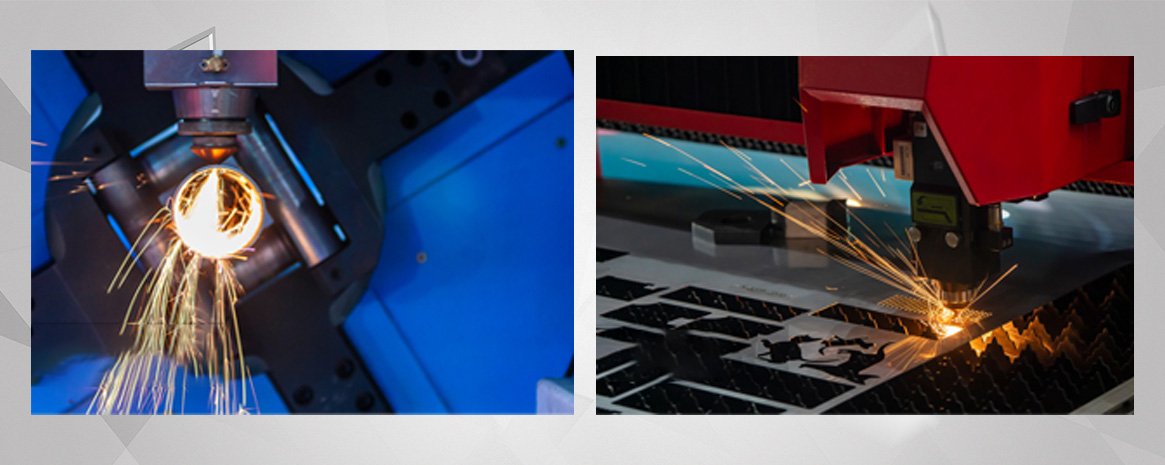
The processing system of the
laser cutting machine itself is a computer system, which can be easily arranged and modified, and is suitable for personalized processing, especially for some sheet metal parts with complex contour shapes. Due to the large number of batches, the product life cycle is not large. Long, from the perspective of technology, economic cost and time, manufacturing molds is not cost-effective, and laser cutting is more advantageous.