1. Properties of the material to be cut
Wood cutting objects are solid wood and wood composite materials.Solid wood can be divided into soft wood, hard wood and modified wood.Wood composite materials include veneer laminated timber, plywood, particleboard, directional particleboard, large particleboard, gypsum particleboard, cement particleboard, hard fibreboard, medium density fibreboard, high-density fibreboard, joinery board, gluing and so on.Some wood or wood composite material work pieces also through one or two - sided veneer decorative processing.
2. Cutting direction
When cutting solid wood, according to the direction of the blade relative to wood fiber, wood cutting is divided into longitudinal, transverse, end and longitudinal, longitudinal and transverse
3, tool rotation direction and feed direction
According to the rotation direction of the tool shaft and the direction of the wood workpiece feed, determine the tilt direction of the edge on the tool.
4. Tool and workpiece stability
The stability of the tool and the workpiece in the cutting process includes several aspects, the stability of the workpiece refers to the wood workpiece in the cutting process smoothly feed without beating to strengthen the stability of the workpiece to take measures mainly to reduce the workpiece center of gravity and increase the contact area.
5. Machining surface quality requirements
The surface quality of wood workpiece includes surface roughness, geometric dimension and shape and position accuracy.
How to reduce the wood engraving machine tool beat
In the process of processing, if the center of the tool and woodworking engraving machine spindle rotation center is not consistent will cause the radial beat of the tool, that is, we usually say that the tool rotation different center.Further understanding is that the normal high speed rotation of the tool should be a vertical line, different hearts will become a cone.In this way machining accuracy and effect must be reduced, the tool will be easy to break so how to reduce the radial runout of the tool processing.
First of all, we should be clear about the mating of the cutter and chuck, the mating of the chuck and nut, whether the knife method is correct and the quality of the tool itself are all factors affecting the runout.In this respect we should pay attention to the chuck and nut clean, no dust.Apply the knife with the correct force, too much or too little is not good.It is also very important that the length of the tool should be small.When necessary, the spindle motor speed should also be noted. For materials that do not require high spindle speed, such as copper, we can choose a reasonable spindle speed to reduce the radial runout
Secondly, how to reduce the radial run-out of the tool during machining.Why does radial run-out occur when a tool is being machined?It is because the radial cutting force intensifies the radial runout that reducing the radial cutting force is an important principle to reduce the radial runout.Using sharp knives, sharp cutting tool for processing the whole cutting force is small, this tool by the radial cutting force is small, so it can reduce the radial runout of cutter tool rake face to smooth: so when processing, can reduce the friction scraps of cutting tool, it can also reduce the tool by cutting force, and reduces the radial runout of the cutting tool;Use reverse milling in finishing: note that this is only used in finishing, rough machining or to use the use of milling, otherwise the service life of the tool is difficult to be guaranteed.When using reverse milling, the direction of the cutting force will always pull the tool towards the workpiece, so that the tool in the process is more stable;Then is the use of a strong woodworking engraving machine tool, increase the strength of the knife by increasing the diameter of the knife rod, the diameter of the knife rod increase by 20%, under the same radial cutting force, the radial tool can be reduced by 50%.
1, the size of the jacket should be appropriate, there is a section, not round, wear, taper hole of the jacket must not be selected, otherwise it will cause a stir, carve the role of ambition.
2. The handle should touch the jacket gently, and the handle should be firmly inserted into the jacket and fastened. If the jacket is deformed after too long operation time, it is necessary to replace the jacket immediately.
3, the tool to often watch patience, if the use of blunt, please immediately replace, if the continued use of not only carve the effect is not good, but also attack the condition of broken knife.
4, woodworking engraving machine operation to be ordered, the thickness of the processing can not exceed the cutting edge of the thickness, as will still appear broken knife.
5, for the cutting of different materials, probably reasonable use of cutting speed.
6, the body, clothes, hair should not be close to the work of objects
7, cutting speed to adhere to the balance, speed as far as possible to adhere to the same, ability to reach a very good role, cutting too long can not stay, to strike while the iron is hot.
8, cutting tools to use a special cleaner to remove dirt.
9. Butter prevents the tool from rusting.
10. The cutter cannot polish itself or change the shape.
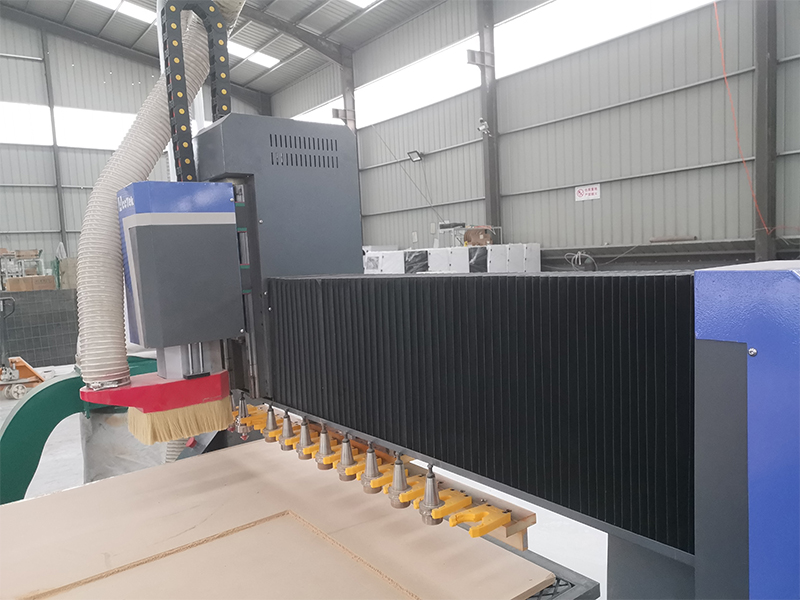